Unternehmen entsprechend der Rangfolge
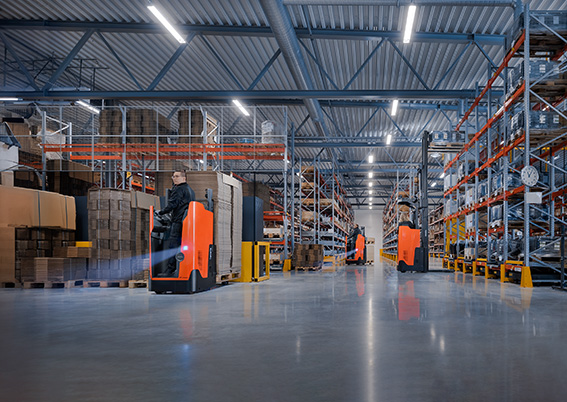
Unternehmen entsprechend der Rangfolge
Hansa-Flex eröffnete anlässlich des 60. Unternehmensgeburtstag neben einer erweiterten Unternehmenszentrale auch ein zusätzliches Logistiklager (Automatisches Palettenlager).
Die Swan GmbH gibt die Gründung ihrer neuen Abteilung „Products & Innovation“ bekannt.
Die Zimmer Group freut sich, die Eröffnung ihrer neuesten Produktionsstätte in Kikvi in der Nähe von Pune, Indien, bekannt zu geben.
Cab Produkttechnik, Hersteller von Etikettendrucksystemen, stellt Hermes QL vor.
Yale Lift Truck Technologies hat sein Angebot an flexiblen Lagertechnikstaplern erweitert.
Platz und Personal werden in der Logistik immer knapper. Prozesse wie das Vereinzeln von Paketen müssen daher automatisiert werden.
Igus hat im März 2024 die mehrheitlichen Anteile am portugiesischen Atronia Tailored Sensing erworben.
Jung Hebe- und Transporttechnik freut sich, dass das Unternehmen sein Angebot durch die Aufnahme des deutschen Exklusivvertriebes der leistungsstarken Transportplattformen des spanischen Herstellers Eyher SL erweitern konnte.
Mit zahlreichen Höhepunkten ist die vierte Auflage des Test Camp Intralogistics zu Ende gegangen.
Mit dem FluX 45 präsentiert Hubtex seinen neuen Elektro-Mehrwege-Gegengewichtsstapler im Tragfähigkeitsbereich bis zu 4,5t.
Lagerverwaltungssoftware revolutioniert die Art und Weise, wie Unternehmen ihre Lagerbestände organisieren, verfolgen und optimieren, indem sie effiziente Prozesse, Echtzeit-Daten und automatisierte Funktionen bereitstellt. Letztendlich ermöglicht eine effektive Lagerverwaltungssoftware Unternehmen, flexibler zu sein, sich schneller an sich ändernde Marktbedingungen anzupassen und somit rentabel und wettbewerbsfähig zu bleiben und nachhaltig zu wachsen. Trotz Vorteilen, die auf der Hand liegen, sind die mit der Implementierung verbundenen Kosten und Prozessumstellungen nicht selten eine Hemmschwelle, die Unternehmen überwinden müssen. Ferag.doWarehouse ist eine innovative Software, welche die Standards für die Lagerverwaltung neu definiert. Sie bietet eine ebenso unkomplizierte wie maßgeschneiderte Lösung für Unternehmen jeder Größe und Komplexität.
Im Oktober 2022 konnten die ZSC Lions ihr neues Heimstadion einweihen. Die Swiss Life Arena ist nicht nur eines der größten Eishockeystadien der Schweiz, sondern vor allem auch eine Multifunktionsarena mit modernster Infrastruktur für die unterschiedlichsten Events und Anlässe. Zur Ausstattung gehört ein Rigging-System an der Hallendecke, das in Zusammenarbeit mit den Firmen B+T Bild+Ton und GIS realisiert wurde. Es besteht aus sechs Traversen und insgesamt 30 Elektrokettenzügen, die bequem über einen Touch-Controller gesteuert werden können.
Porsche bindet in der Intralogistik Automated Guided Vehicles (AGVs) ein, die ab sofort über den MHP FleetExecuter gesteuert werden. Damit setzt der Autobauer erstmals in der Unternehmensgeschichte auf eine zentrale Flottenleitsteuerung. Die in die bestehende IT-Infrastruktur integrierte Cloud-Lösung ist in den Stammwerken in Zuffenhausen im Einsatz. Dort dient sie als funktionaler Core der Automatisierung des Logistikprozesses. In Kürze sollen weitere Roll-outs folgen, etwa beim Bau des Taycan. Geplant sind zahlreiche Projekte, bei denen insgesamt mehrere hundert Fahrzeuge in unterschiedlichen AGV-Flotten mit über 300 Funktionen im Einsatz sind. Die Tochtergesellschaft von Porsche ist dabei für Beratung, Implementierung, Produktentwicklung sowie Service und Support verantwortlich.
Die Adnymics GmbH, ein Technologieanbieter für individualisierte Paketbeilagen, wird vom niederländischen Marketing-Kollektiv Linehub übernommen.
Die fortschreitende industrielle Automatisierung hat ein neues Stadium erreicht: Autonome mobile Roboter (AMR) sind mittlerweile aus Produktionshallen und Logistikzentren weltweit nicht mehr wegzudenken. Diese Technologie ermöglicht es Unternehmen, eine breite Palette von Aufgaben und Prozessen zu automatisieren, was zu einer signifikanten Steigerung der Produktivität und wirtschaftlichen Widerstandsfähigkeit führt. Doch gleichzeitig müssen wir uns den neuen Sicherheitsherausforderungen stellen, die mit der Integration dieser Systeme einhergehen. In diesem Zusammenhang stellt sich die zentrale Frage, wie AMR dazu beitragen können, die physischen Sicherheitsstandards in der Industrie zu erhöhen und gleichzeitig die Resilienz gegenüber Cyberangriffen zu stärken.
Die Vandemoortele Group setzt für die digitale Transformation in der Kommissionierung auf die Workflows der Augmented-Reality-Plattform (AR) Teamviewer Frontline.
Der Logistik- und Transportdienstleister Prévoté modernisiert die Bestandsverwaltung mit ZetesMedea Full Pallet Inventory.
Zwei international tätige Automatisierungsspezialisten unterzeichneten vor Kurzem eine strategische Partnerschaft.
Ob Automobil- oder Flugzeugproduktion – FFT gilt als weltweit führender Systemanbieter von schlüsselfertigen Produktionsanlagen.
Roboter bewegen in der industriellen Produktion viele verschiedene Gebinde.
Unternehmen entsprechend der Rangfolge
Die Anforderungen an Lagerbetreiber bewegen sich heute zwischen maximaler Effizienz des Lagerbetriebs bei gleichzeitig höchster Nachhaltigkeit der Intralogistik. KI-basierte Digitalisierung und Automatisierung sind aktuelle Trendthemen, um beiden Ansprüchen gerecht zu werden. Empfiehlt es sich gleich das komplette Logistikzentrum zu automatisieren oder nur einzelne Teilbereiche – und wie lässt sich dabei gleichzeitig noch der CO2-Fußabdruck reduzieren? In der großen dhf Intralogistik-Herstellerumfrage 2023 geben Hersteller und Anbieter von Lagerlogistik-Lösungen Antworten auf diese Fragen sowie eine Einschätzung der Marktentwicklung in den kommenden Jahren.
Künstliche Intelligenz, kurz KI, ist rasant im Kommen – auch in der Intralogistik. Der Grund ist verständlich, denn der Einsatz von KI-basierter Software verspricht optimierte Prozesse in der Lagerlogistik, damit eine höhere Effizienz und eine bessere Nachhaltigkeit im Betrieb, sowie perspektivisch auch ein lukrativeres Kostenmodell. Moderne Warehouse Management Systeme (WMS) schaffen die Voraussetzung, das Potenzial dieser Technologie praktisch per Knopfdruck oder Mausklick zu erschließen. Mit welchen konkreten Software-Lösungen und intelligenten
Features WMS-Anbieter aktuell ihre Kunden unterstützen und in welche Richtung die nächsten Entwicklungsschritte gehen, zeigt die jüngste Herstellerumfrage von dhf Intralogistik.
Omron freut sich, die Ernennung von Dr. Lucian Dold zum Senior General Manager für Global Account Business Development bekannt zu geben.
Vom Werkstattbetrieb zum Weltmarktführer in wichtigen Feldern der Befestigungstechnik – so lässt sich die erfolgreiche Entwicklung des Familienunternehmens Fischer seit seiner Gründung 1948 zusammenfassen.
Puls, ein Technologie- und Marktführer im Bereich DIN-Schienen Stromversorgungen, hat das Geschäft des Wireless-Charging-Spezialisten Wiferion übernommen.
Ab 1. Oktober 2023 organisiert Faulhaber seine Vertriebsorganisation neu und legt den Schwerpunkt dadurch noch stärker auf Kundenorientierung und schnelle Reaktionsfähigkeit.
Der schnell wachsende E-Commerce-Sektor, insbesondere im Modebereich, konfrontiert die Fulfillment-Center mit erheblichen Herausforderungen. Dazu zählen nicht nur erhöhte Service-Erwartungen, sondern auch die komplizierte Abwicklung von Retouren. Eine fortschrittliche Lösung besteht darin, Taschensorter-Systeme einzuführen.
Langlebigkeit, Nachhaltigkeit, Umweltverträglichkeit: Bei (intra-)logistischen Prozessen rund um Herstellung, Transport und Lagerung gelten neue Maßstäbe – auch für Ladungsträger. Von hoher Qualität, langlebig, strapazierfähig, vielseitig, wartungsfrei und recycelbar, das sind die Eigenschaften von Paletten und Behältern, die eine nachhaltige und wirtschaftliche (Lager-)Logistik ermöglichen. Als einer der führenden Hersteller von langlebigen Logistik-Lösungen mit über 60 Jahren Erfahrung in der Kunststoffverarbeitung entwickelt und fertigt die Craemer Gruppe hochwertige Mehrwegladungsträger mit genau diesen Merkmalen. Paradebeispiel ist die Kunststoffpalette Euro L1 – aus Kunststoff statt Holz. Bei der Produktion ihrer Kunststoffprodukte setzt die Unternehmensgruppe verstärkt auf selbsterzeugtes Rezyklat und regenerative Energien.
Bodenbündige Schienensysteme eignen sich nicht nur für Fertigungslinien im Anlagen- und Maschinenbau oder die Präzisionsbeschickung von Werkstücken an Schweißzellen und Schneidanlagen. Sie lassen sich ebenso gut für die Lagerlogistik und das effiziente Materialhandling tonnenschwerer Lasten einsetzen. Ein Beispiel dafür ist das beim Bielefelder Maschinenbauzulieferer Dreckshage neu installierte LOXrail-System für Traglasten bis 15t, auf dem Rohrgebinde
und andere schwergewichtige Werkstoffe einfach per Hand von einer Lagerhalle zur nächsten verfahren werden.
Das Sauerländer Traditionsunternehmen Gebrüder Schulte präsentiert sich 2024 digital und analog erstmals mit einem neuen, zukunftsweisenden Gestaltungssystem und dem selbstbewussten Claim „Wir regalen das“. Mit dem nutzerfreundlichen Markenauftritt schafft Schulte an allen Touchpoints relevante Mehrwerte und kreative Freiräume für seine Kunden. Gleichzeitig setzt das Unternehmen damit
ein Zeichen für seine bekannte Innovationskraft und den Mut zur Veränderung.
Die Ansprüche an die Umschlagsleistung in der Logistikbranche steigen
stetig. Um diese Herausforderungen meistern zu können, bietet SEWEurodrive unterschiedliche, skalierbare Lösungen für den Sorter und
dessen Zuführung, auch Infeed genannt.
Ordnung ist mehr als nur das halbe Leben. Das zeigt sich insbesondere bei der Sortierung von Paketen im Logistikzentrum. In Greven hat DHL Home Delivery das Paket-Nadelöhr deshalb mit einem Celluveyor Crossdock von Cellumation beseitigt. Die automatisierte Sortierung ist flexibel und löst Knotenpunkte im Materialfluss. Mit der neuen Lösung konnte DHL die Anzahl der stündlich sortierten Pakete um 40 Prozent steigern. Das hilft dem Paketzentrum dabei, in Spitzenzeiten mehr als 600.000 Sendungen umzusetzen.
Vier Jahre nach der Produktvorstellung performt der Transportroboter Vario Move nicht nur auf der Logimat-Messe mit beeindruckenden Lastspielen: Auch in vielen Branchen und unterschiedlichen Unternehmensgrößen hat sich die Transportroboterserie mit ihrer Vielseitigkeit und Zuverlässigkeit durchgesetzt.
Neura Robotics, ein globaler Pionier im Bereich der kognitiven Robotik, und Omron Robotics and Safety Technologies Inc, ein weltweit agierender Anbieter von Industrierobotik und -automatisierung, freuen sich, ihre strategische Partnerschaft bekannt zu geben.
Der Augsburger Automatisierungsexperte Kuka und der Wolfsburger Automobilkonzern Volkswagen haben eine Rahmenvereinbarung über die Lieferung von mehr als 700 Robotern in diesem und den kommenden beiden Jahren geschlossen.
Der Hamburger Intralogistikanbieter Still baut sein Servicekonzept konsequent aus und macht schnellen und flexiblen Vor-Ort-Service künftig auch für automatisierte Fahrzeuge möglich.
Linde Material Handling (MH) modernisiert den Standort in Kahl am Main mit dem Neubau eines hochautomatisierten Distributionszentrums für Ersatzteile. Auf 21.000m² Fläche entstehen unter anderem ein vollautomatisches Hochregallager mit 30m und ein Multishuttle-Lagersystem. Die geplante Investitionssumme liegt bei 60 Millionen Euro, 2025 soll das neue Verteilzentrum seinen Betrieb aufnehmen. Das Materialflusskonzept des Regional Distribution Centers (RDC) wurde in einem mehrstufigen Analyse- und Optimierungsprozess entwickelt. Am Ende stand eine Lösung, die den Anforderungen an Effizienz, Verfügbarkeit und Produktivität bestmöglich Rechnung trägt.
Als Hersteller von Malzen und Backzutaten ist Stamag Stadlauer Malzfabrik ein wichtiger Partner von Brauereien und Bäckereibetrieben. Deren Gläserne Backzutatenmanufaktur in Wien ermöglicht die flexible und zugleich hygienische Zusammenstellung der Backmischungen nach rund 400 Rezepturen. Das Rückgrat der im Jahr 2023 eröffneten Produktionsstätte bilden zwei fahrerlose Transportsysteme von
DS Automotion.
Das Lager der Zukunft wird auf die Integration und Optimierung von Logistikfunktionen bauen, die schrittweise verbessert werden und die Fähigkeit erhalten, in jedem Bereich, vom Wareneingang bis zum Versand, Daten zu sammeln und auszuwerten. Die industrielle Bildverarbeitung wird dabei eine wichtige Rolle spielen.
Deutsche Industrie Video System, ein auf visuelle Sendungsverfolgung spezialisiertes Technologieunternehmen (Divis), ist eine strategische Partnerschaft mit Metrilus eingegangen. Als Marktführer im Bereich Computer-Vision-basierter Frachtvermessungssysteme entwickelt Metrilus Software für 3D-Kameras, die zur Verbesserung der Datenqualität weltweit in der Logistikbranche zum Einsatz kommen. Gegenstand der Partnerschaft ist die Integration der Volumenmesstechnologie MetriXFreight in die softwarebasierten Videomanagementsysteme von Divis.
Eine unterbrechungsfreie Produktion hat für fertigende Unternehmen oberste Priorität. Doch der Austausch wichtiger Peripheriegeräte kann den Zeitplan empfindlich stören. Für die reibungslose Modernisierung seiner Druckerflotte setzte der Sonnenschutzsystem-Hersteller Roma daher auf Geräte von TSC Printronix Auto ID. Um plötzlich ausfallende Drucker schnell ersetzen zu können, hat TSC zudem den neuen Printer Setting Replicator entwickelt. Dieser ermöglicht die einfache, schnelle und flexible Übertragung von Druckereinstellungen zwischen vorhandenen Geräten.
Die Automatisierungsexperten von Omron präsentieren den neuen Handheld-Scanner V450-H.
Pierre Mikaelsson steigt als neuer Chief Product Officer (CPO) bei ProGlove ein und leitet ab sofort die Produktentwicklung.
dhf Intralogistik TV war auf der Logimat am Stand von CCL Faubel und hat mit Andreas Bartling, Business Development Manager, über die Logistics Labels – digitale Kennzeichnungen für Boxen, für Container – des Unternehmens gesprochen.
Wer seine Produkte in die ganze Welt verschickt, muss sicher sein können, dass sie ihr Ziel auch unbeschadet erreichen. An einer Transportsicherung führt deshalb kein Weg vorbei. Mögliche Lösungen reichen vom einfachen Verpackungsband bis zur kompletten Umreifungsanlage. Energieketten
aus Stahl von Tsubaki Kabelschlepp sorgen für eine sichere und präzise
Führung aller Medien an diesen Maschinen und ermöglichen auch unter rauen Bedingungen einen zuverlässigen Prozess bei hoher Verfügbarkeit.
Konecranes definiert mit dem Kran der X-Serie und der innovativen S-Serie niedrige Bauhöhe die Zukunft der Hebetechnik neu. Die neuen Hebesysteme sind ein Paradebeispiel für Ingenieurskunst, die sich durch Anpassungsfähigkeit, intelligente Technologien und Nachhaltigkeit auszeichnet.
Die Unternehmensgeschichte von SWF Krantechnik ist geprägt von einer über hundertjährigen technologischen Evolution, stetigem Wachstum und kontinuierlicher Innovation im Bereich der Hebezeugindustrie sowie dem damit verbundenen Material- und Informationsfluss. Im Laufe der Jahrzehnte entwickelte sich das Unternehmen zu einem namhaften Anbieter für Komponenten für Industriekrane und Hebezeuge. SWF Krantechnik setzt bis heute immer wieder Akzente im Markt.
Ob Paletten, Kartonagen oder Sackwaren – Vakuum-Schlauchheber eignen sich für Güter aller Art. Nicht zuletzt aufgrund ihrer Flexibilität sind sie aus der Intralogistik nicht mehr wegzudenken – und sorgen für mehr Ergonomie am Arbeitsplatz. Hebetechnik-Spezialist Timmer bietet mit seinem umfassenden Portfolio an Schlauchhebern Lösungen für unterschiedlichste Anwendungsfelder. Dank umfangreichem Zubehör sind die Hebehilfen über den klassischen Einsatz in der Intralogistik hinaus auch für spezielle Anwendungen geeignet wie beispielsweise in der Lebensmittelverarbeitung und in Bereichen, die potenziell explosionsgefährdet sind.
Schwer zugängliche Lasten in einer Höhe von 3,5m bewegen, die teilweise nur über Wege mit einer Durchfahrthöhe von 1,95m erreichbar sind – vor
dieser Herausforderung stand Industriekran-Hersteller Siegfried Frenzen bei einem Kunden, der im Handel mit Lebens- und Futtermitteln sowie nachwachsenden Rohstoffen tätig ist.
Das traditionsreiche und innovative Familienunternehmen aus der Werkzeugstadt Remscheid im Bergischen Land ist mit seinen Kranen und Krankomponenten weltweit vertreten. Produkte von Kuli mit über 100 Jahren Erfahrung sind in Branchen von „A bis Z“, von der Automobilzulieferung bis zur Zementindustrie, in über 120 Ländern und auf allen Kontinenten im Einsatz.
Ob bei Aufmaß, Montage, Inbetriebnahme oder Wartung – die neuen, mobil einsetzbaren digitalen Tools und Services von Novoferm vereinfachen die Prozesse vor Ort erheblich. Das gilt sowohl auf der Baustelle als auch im Objekt.
Am 1. Januar 2024 übernahm Bettina Baumann nach erfolgreich abgeschlossenem Studium die Geschäftsführung des Münchner Logistikunternehmens Baumann Paletten.
Frage: Wie viele Jahre dürfen Hebebänder oder eine Rundschlingen verwendet werden?
Chep, Experte im Pooling von Paletten und Behältern, ist neues Mitglied des Verbands Klimaschutz-Unternehmen e.V.
Auf dem Logistik-Yard von BSH Hausgeräte in Giengen an der Brenz wird mit Hochdruck an Zukunftsthemen des Frachtverkehrs geforscht. Davon machten sich Vertreterinnen und Vertreter von Politik und Wirtschaft nun bei einer Live-Demonstration ein Bild.
Mit neuen digitalen Tools öffnet Novoferm Tür und Tor für mehr Planungssicherheit und Effizienz. Neben dem praktischen Lösungsgenerator und dem neuen Service-Dashboard bietet das Unternehmen weitere neue App-Lösungen und smarte Tools. Sie alle haben eines gemeinsam: Sie vereinfachen Prozesse und beschleunigen Arbeitsabläufe.