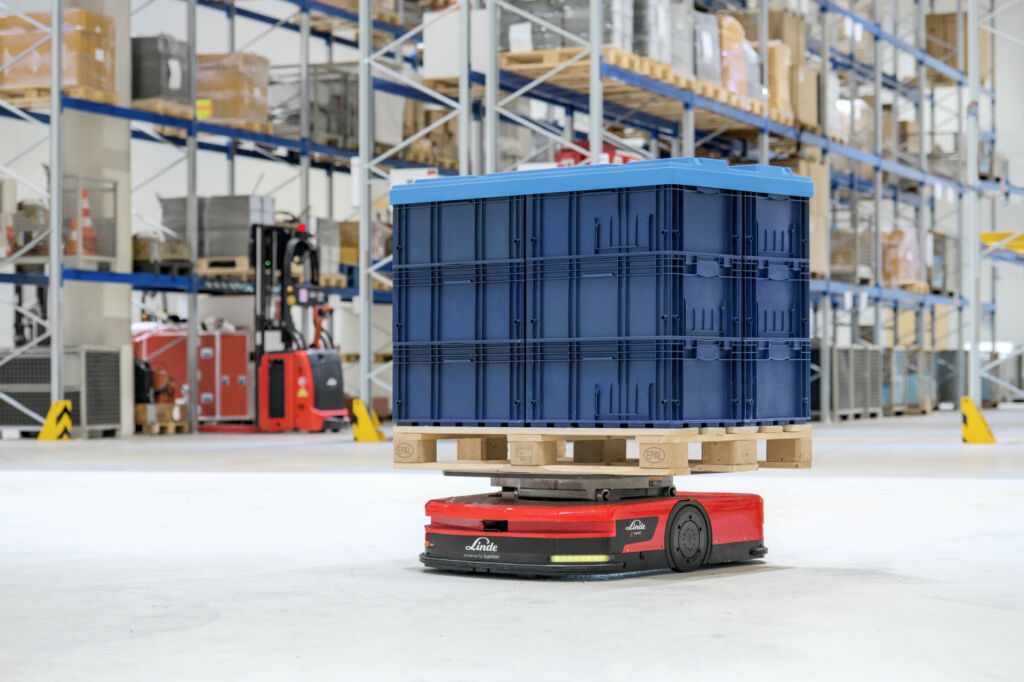
Der neue Gebäudekomplex auf dem großen Areal nimmt bereits erkennbar Gestalt an und die Bauarbeiten laufen im Zeitplan. Das neue Verteilzentrum mit zentraler Lage in Europa ist ein wichtiges Projekt für Linde MH und legt die Basis für zukünftiges Wachstum. Netzwerkpartner und Kundenunternehmen sollen Ersatzteile für die steigende Zahl an Fahrzeugmodellen und Ausstattungsoptionen noch schneller zur Verfügung haben, damit Flurförderzeuge wegen Wartungs- oder Reparaturarbeiten so kurz wie möglich stillstehen. Doch nicht nur leistungsstark und erweiterungsfähig soll das RDC sein, sondern auch umwelt- und klimafreundlich. Durch verschiedene Maßnahmen werden die Vorgaben des Gold-Standards der Deutschen Gesellschaft für Nachhaltiges Bauen (DGNB) erfüllt. Geplant ist eine PV-Anlage zur Stromerzeugung, Regenwasser soll als Brauchwasser genutzt oder das Dachwasser in den nahgelegenen See und nicht in die Kanalisation geleitet werden. Hinzu kommen Ausgleichsmaßnahmen für den Natur- und Artenschutz.
Nach seiner Fertigstellung wird das RDC mehrere Bereiche für den Warenein- und Warenausgang, Kommissionierzonen sowie ein Block- und Sonderlager umfassen. Die Andienung erfolgt über 16 Lkw-Rampen. In den Materialfluss integriert sind u.a. Stetigförderer für Klein- und Großteile von Dematic und AMRs (Autonomous Mobile Robots) sowie manuell bediente Elektrogegengewichtstapler und Hochhubwagen von Linde MH. Dematic liefert außerdem das vollautomatische Hochregallager mit sechs Gassen und das Multishuttle-Lager, in dem in fünf Gassen rund 110.000 Stellplätze angesteuert werden.
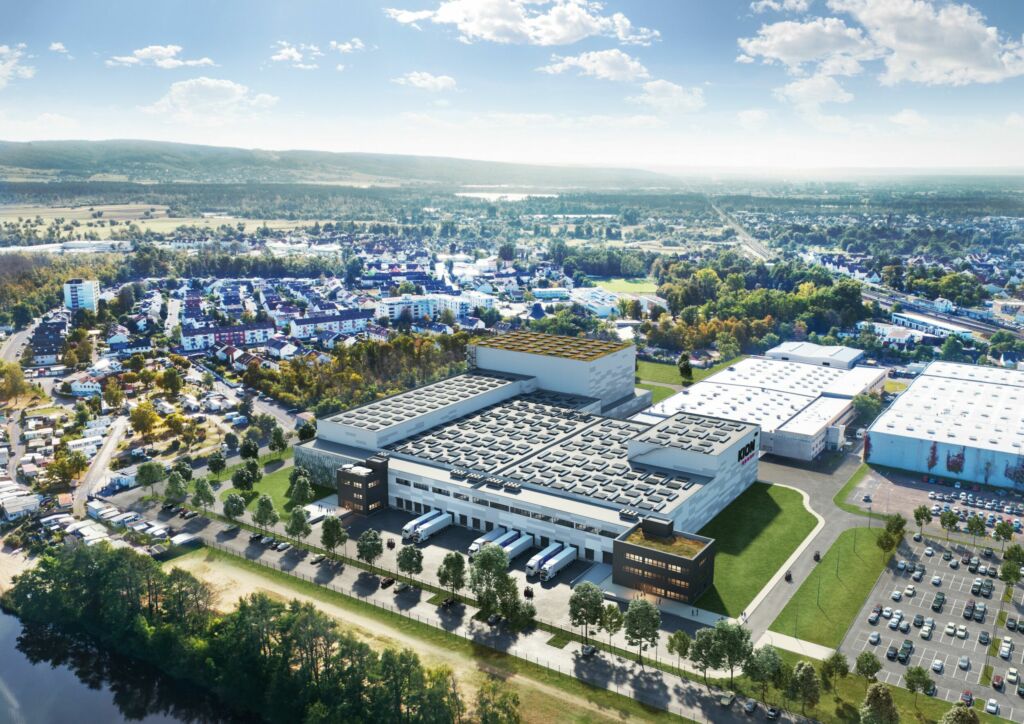
Übergreifende Kooperation für ganzheitliche Lösung
Aufgrund der komplexen Anforderungen war das Bauvorhaben geradezu prädestiniert für ein gemeinsames Projekt von Linde MH und Kion-Konzernschwester Dematic. Beide Unternehmen kooperieren am Markt in gleicher Weise bei anspruchsvollen Kundenprojekten, wo sowohl integrierte Automatisierungstechnik als auch autonome mobile Roboter (AMRs) und automatisierte Flurförderzeuge zum Einsatz kommen.
Begonnen wurde das Großprojekt mit einer detaillierten Definition des geforderten Leistungsumfangs sowie den funktionalen Eigenschaften der Materialflusslösungen. Ebenso galt es, alle Fachdisziplinen personell adäquat zu besetzen sowie einen kontinuierlichen Kommunikationsfluss zwischen den Projektbeteiligten zu etablieren. Dazu gehören wöchentliche Meetings, um offene Punkte zeitnah zu klären und bei allen Maßnahmen die Gesamtkosten im Blick zu behalten.
Erste große Aufgabe des Projektteams war die Planung des Lagerlayouts mit dem dazugehörigen Materialflusssystem. Alle wussten um die weitreichenden Konsequenzen. Denn sind Lager- und Systemlayouts erst einmal festgelegt, lassen sich Änderungen in der Bauphase nur noch bedingt und mit zusätzlichen Kosten umsetzen. Soweit wie möglich sollte der Materialfluss automatisiert erfolgen, um die hohen Anforderungen an Effizienz und Produktivität bestmöglich zu erfüllen. Wie bei allen Automatisierungsprojekten empfohlen, wurden die Bedarfe systematisch analysiert und Simulationen durchgeführt. Doch ebenso erfolgsentscheidend war die Bereitschaft in der Vorbereitungs- und Planungsphase, die zunächst gefundenen Ansätze und Konzepte noch einmal in Frage zu stellen und Alternativen zu prüfen. So geschehen beim neuen Verteilzentrum für Ersatzteile.
Rückgrat des Materialflusssystems
In einem Workshop wurde das Systemdesign hinterfragt bzw. herausgefordert und in der Tat daraufhin an einigen Stellen noch einmal umgeplant. Anders als ursprünglich vorgesehen, entschieden sich die Verantwortlichen anstelle einer Palettenförderanlage für eine Elektrobodenbahn (EBB) als Kernsystem der Palettenverteilung. Sie bildet das Rückgrat des gesamten Materialflusssystems. Weiteres Ergebnis der Validierung: Flexible AMRs ergänzen die festeingebauten Automatisierungssysteme und verhindern, dass zentrale Transportachsen im Lager durch fest einbaute Fördertechnik blockiert werden. Die mobilen Roboter übernehmen die Aufgabe, volle Paletten vom Wareneingang in Richtung Hochregallager bzw. zur Qualitätssicherung zu transportieren und leere Paletten und Gitterboxen zu retournieren. Kostspielige Liftsysteme für diese Materialflüsse konnten auf diese Weise vermieden werden.
Eine weitere Überprüfung ergab, dass die Regalbediengeräte im Hochregallager nicht auf alle Paletten direkt zugreifen müssen, sondern Paletten auch in zweiter Reihe stehen können. Nun kommt ein doppeltiefes Lagersystem zum Einsatz, wodurch sich Ersparnisse bei den Regalbediengeräten und beim Regalsystem erzielen ließen, ohne Abstriche bei der Effizienz zu machen.
Hocheffizientes Multishuttle-System
Bestätigt wurde hingegen die Wahl des Multishuttle-Systems als effizienteste Möglichkeit, Kleinteile zu lagern und bereitzustellen. Doch auch hier konnte im Detail optimiert werden. So entsteht das aufgeständerte Multishuttle der neuesten Generation von Dematic in Silobauweise. Die Besonderheit: Das Regalsystem bildet gleichzeitig das tragende Element für die Außenhülle mit Fassade, wodurch sich positive Effekte für Bauzeit und -kosten ergeben. Direkt unter dem Multishuttle befinden sich zudem Arbeitsplätze für Pack- und Kommissioniertätigkeiten.
Das Beispiel RDC zeigt, welche Bedeutung der Planungs- und Vorbereitungsphase bei Automatisierungsprojekten zukommt. Hier unterschiedliche Alternativen zu prüfen, um am Ende die richtigen Weichen zu stellen, ist von entscheidender Bedeutung. Beim neuen RDC in Kahl sind sich die Verantwortlichen einig, das für den vorliegenden Einsatzfall beste Konzept gefunden zu haben.
((Kasten))